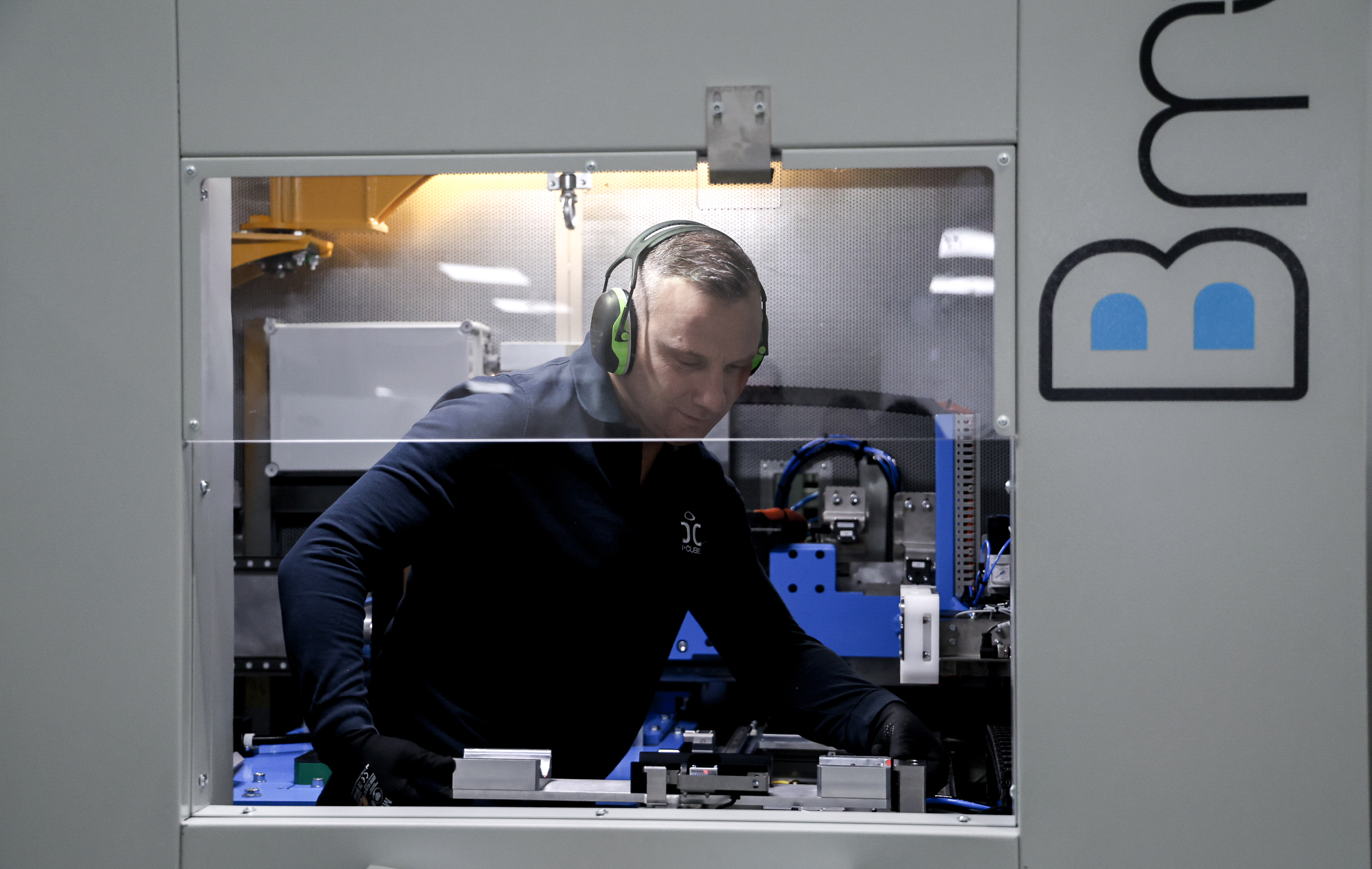
The conductive part is placed inside or next to a coil which accelerates it over 1mm to impact the second workpiece at extremely high speed. The acceleration is a result of repelling magnetic fields between the workpiece and the coil, produced by the eddy current in the workpiece.
Solid state cold weld is created when two metals are forced together in such intensity that their atoms start sharing electrons, practically welding the two metals together. MPW trig-gers this phenomenon when the accelerated part impacts the other workpiece at speed above 300m/s, placing them into a viscoplastic phase and with the proper impact angle, create conditions to get such a cold weld.
Benefits Of Magnetic Pulse Welding
Green & Clean Process
- Uses low amounts of energy
- No heat, no sparks, no smoke, no radiation
- No cleaning or treatment required for the part before or after welding
Lower Costs
- Lower Total Cost of Ownership (TCO) vs conventional welding techniques
- Reduces component thicknesses, resulting in weight and cost savings and lower product CO2 footprints
Product Performance
- Since there is no heat or melting involved, dissimilar metals can be welded together. Many welding combinations using dissimilar metals are possible, as long as one of the two materials has good electrical conductivity.
- High weld mechanical strength: typical joints are stronger than the parent materials (no heat affected zone)
- High quality, very aesthetic and extremely clean interface, with no joint distortion
- Limited corrosion development in the welding area
Process Performance
- Can replace TIG welding, laser welding, ultrasonic welding or brazing
- No heat, no filler material, no inert gas are required
- Parts can be handled immediately after the welding (cold weld)
- Excellent repeatability and Low scrap rate
- High-speed (a typical pulse lasts from 10 to 100µs, so the only time limitation is loading and unloading)
- Reliable and well suited to high-volume production
- Quick change over, resulting in time savings
Premium Technology
Magnetic Pulse Welding | Conventional Welding | |
Welding Technology | Cold Welding, <br>No Heat-Affected Zone | Fusion Welding |
Weld Strength | No degradation of materials’ properties | Heat-Affected Zone inherently makes weak seams |
Weight Saving | >20% weight reduction | Extra material thickness required due to embrittlement of materials |
Disimilar Marerials | Wide range of material combination: Al/SS, Al/Cu, Al/St, etc. | Not possible |
Process Cleanliness & Simplicity | <center>-</center> | Pre/post treatments <br>Use of inert gas <br>Very precise positioning<br>Laser beam safeguarding<br>Special anti-radiation enclosure |
Scrap Rate | <0.1% | 3-5% |
Energy Consumption | < 6kW | >60% more consumption |
Consumables | <center>-</center> | Inert gas and a lot of other consumables are required |
Weld Quality & Aspect | Excellent quality, very aesthetic with no joint distortion | Joint deformation and distortion, due to heat and residual stress |
Welding System
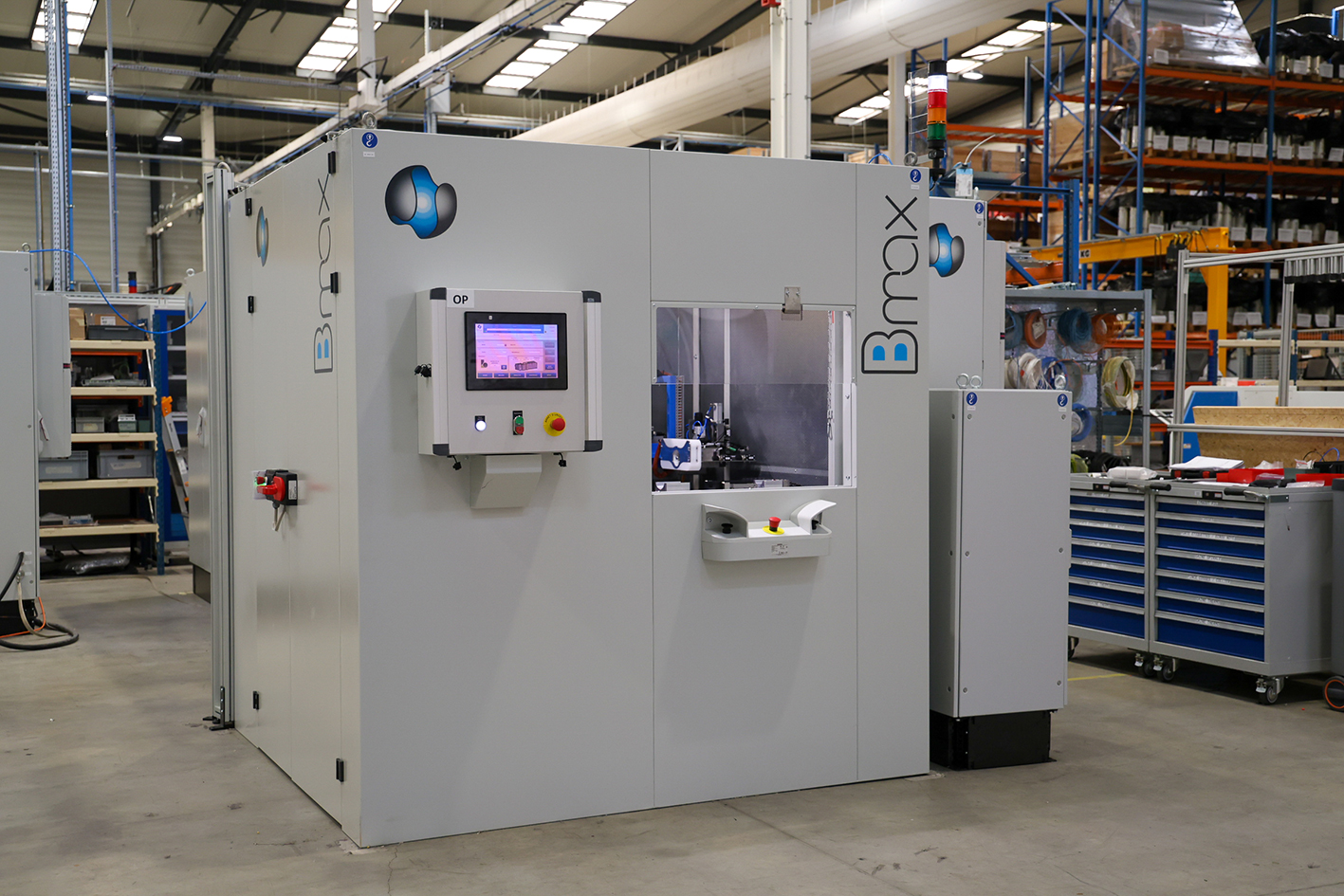
Tube to Cap type Pressure Vessels - e.g. R744 (CO2) Accumulators or R290 (Propane) receiver driers
Tube:
- Dimensions: up to φ100mm & 5mm thick – depending on material grade
- Material grade: Al 6xxx series as a standard – other material possible on demand
Cap:
Material grade: Al 6xxx series as a standard – other material possible on demand
- Embedded with the highest level of machine security in the market
- CE-certified with the support of an independent certification body
- Fully compliant with applicable regulations, technical standards and directives
- EMC and sound proof workstation
- Optimized footprint
- Production throughput: 1,000,000 welds/year
- ≥80% OEE (Overall Equipment Efficiency)
≤20 sec cycle time per weld, with no cooling downtime – Welding time ≤100µs
- Cpk>2
- No mechanical contact between tooling and parts to be welded
- Highly synchronized switches ensuring extremely low variations of electrical signals
- Scrap rate close to 0%
- Fully integrated Process Monitoring System with real time welding data acquisition & recording
- Real-time detection of defective weld
- Stand-alone, turnkey system, easy to install in any industrial environment
- User-friendly HMI
- Easy access to product positioning cart
- Secured access doors to perform maintenance operations
- Integrated lifting devices, enabling ergonomic, safe and easy maintenance
- ≤15min tool changeover time
- Remote assistance/maintenance capability
- Optional diagnosis function
- Low electrical power consumption <6kW (production mode)
- No filler material, no toxic fumes, no dangerous radiation
- No need for cleaning the parts, neither before nor after welding